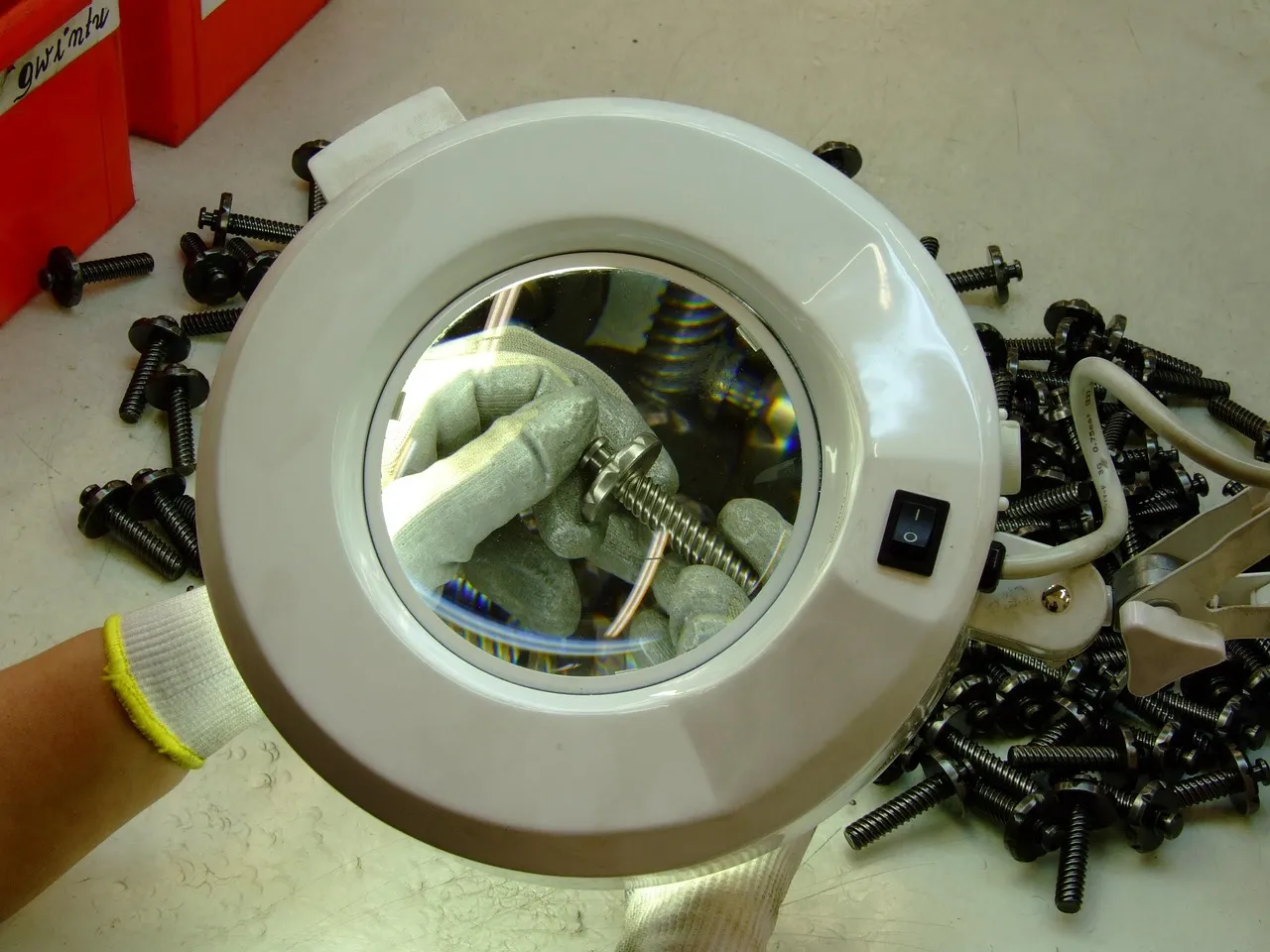
Wie die Cpk-Werte die Prozessqualität verbessern
Die Qualität von Produktionsprozessen spielt eine entscheidende Rolle in der heutigen industriellen Landschaft. Unternehmen stehen vor der Herausforderung, ihre Effizienz zu maximieren und gleichzeitig die Qualität der Produkte zu gewährleisten. In diesem Kontext gewinnen statistische Methoden zur Prozesskontrolle zunehmend an Bedeutung. Eine der wichtigsten Kennzahlen, die in der Prozessoptimierung verwendet wird, ist der Cpk-Wert. Dieser Wert bietet wertvolle Einblicke in die Fähigkeit eines Prozesses, innerhalb vorgegebener Spezifikationen zu arbeiten.
Die Berechnung und Analyse von Cpk-Werten ermöglicht es Unternehmen, Schwachstellen in ihren Produktionsprozessen zu identifizieren und gezielte Verbesserungsmaßnahmen zu ergreifen. Durch die Anwendung dieser Methoden können nicht nur die Produktqualität, sondern auch die Kundenzufriedenheit und die Wirtschaftlichkeit der Produktion gesteigert werden. In der folgenden Diskussion werden wir die Bedeutung von Cpk-Werten für die Prozessqualität, deren Berechnung und die Implementierung von Verbesserungsstrategien näher betrachten. Unternehmen, die diese Konzepte erfolgreich umsetzen, können sich einen Wettbewerbsvorteil verschaffen und ihre Position auf dem Markt stärken.
Bedeutung der Cpk-Werte in der Prozesskontrolle
Die Cpk-Werte, auch bekannt als Prozessfähigkeitsindizes, sind wesentliche Instrumente zur Bewertung der Prozessqualität. Sie messen die Fähigkeit eines Prozesses, Produkte innerhalb festgelegter Toleranzen herzustellen. Ein hoher Cpk-Wert deutet darauf hin, dass der Prozess stabil und fähig ist, die geforderten Spezifikationen zu erfüllen. Dies ist besonders wichtig in Branchen, in denen hohe Präzision und Qualität erforderlich sind, wie beispielsweise in der Automobilindustrie oder der Medizintechnik.
Ein niedriger Cpk-Wert signalisiert hingegen, dass der Prozess möglicherweise nicht in der Lage ist, die Qualitätsanforderungen zu erfüllen. In solchen Fällen ist es entscheidend, die Ursachen für die Abweichungen zu identifizieren. Häufig sind Variabilität und Ungenauigkeiten in den Produktionsschritten die Hauptgründe für einen niedrigen Cpk-Wert.
Die regelmäßige Überwachung der Cpk-Werte ermöglicht es Unternehmen, Probleme frühzeitig zu erkennen und Anpassungen vorzunehmen. Durch die kontinuierliche Verbesserung der Prozessfähigkeiten können nicht nur Ausschussraten gesenkt, sondern auch die Gesamteffizienz gesteigert werden. In der heutigen wettbewerbsorientierten Geschäftswelt ist die Fähigkeit, qualitativ hochwertige Produkte zu einem wettbewerbsfähigen Preis anzubieten, von größter Bedeutung.
Berechnung und Analyse der Cpk-Werte
Die Berechnung des Cpk-Wertes erfolgt durch die Analyse von Prozessdaten. Der Cpk-Wert wird aus den Prozessmittelwerten und der Standardabweichung ermittelt. Die Formel lautet: Cpk = min [(USL – μ) / (3σ), (μ – LSL) / (3σ)], wobei USL die obere Spezifikationsgrenze, LSL die untere Spezifikationsgrenze, μ der Prozessmittelwert und σ die Standardabweichung ist.
Um die Cpk-Werte effektiv zu analysieren, sollten Unternehmen regelmäßig Daten aus ihren Produktionsprozessen sammeln. Diese Daten können durch statistische Software oder einfache Excel-Tabellen ausgewertet werden. Eine Visualisierung der Cpk-Werte im Zeitverlauf kann helfen, Trends zu erkennen und die Auswirkungen von Änderungen im Produktionsprozess zu bewerten.
Darüber hinaus sollten Unternehmen Schulungen für ihre Mitarbeiter anbieten, um das Verständnis für die Bedeutung der Cpk-Werte zu fördern. Eine informierte Belegschaft kann dazu beitragen, die Prozessqualität zu verbessern, indem sie bewusster mit den Produktionsstandards umgeht und aktiv zur Fehlervermeidung beiträgt.
Strategien zur Verbesserung der Cpk-Werte
Die Implementierung effektiver Strategien zur Verbesserung der Cpk-Werte ist entscheidend für die Optimierung der Prozessqualität. Zunächst sollten Unternehmen eine gründliche Analyse ihrer aktuellen Prozesse durchführen, um Schwachstellen zu identifizieren. Methoden wie die Ursachen-Wirkungs-Analyse oder das Pareto-Diagramm können dabei hilfreich sein.
Ein weiterer wichtiger Schritt besteht darin, die Prozessbedingungen zu standardisieren. Durch die Einführung von klaren Arbeitsanweisungen und Prozessen können Variabilitäten reduziert und die Konsistenz der Ergebnisse erhöht werden. Schulungen und Workshops sind ebenfalls entscheidend, um sicherzustellen, dass alle Mitarbeiter die neuen Standards verstehen und einhalten.
Zusätzlich sollten Unternehmen in moderne Technologien investieren, die eine präzisere Prozesskontrolle ermöglichen. Automatisierung und digitale Überwachungssysteme können dabei helfen, Prozessabweichungen in Echtzeit zu erkennen und sofortige Maßnahmen zu ergreifen.
Die kontinuierliche Überwachung und Anpassung der Strategien zur Verbesserung der Cpk-Werte wird letztendlich zu einer höheren Produktqualität, geringeren Kosten und einer steigenden Kundenzufriedenheit führen. Unternehmen, die diese Prinzipien erfolgreich umsetzen, werden sich nicht nur als Marktführer positionieren, sondern auch langfristig erfolgreich sein.
Bitte beachten Sie, dass dieser Artikel keine medizinischen Ratschläge enthält. Bei gesundheitlichen Problemen sollten Sie stets einen Arzt konsultieren.
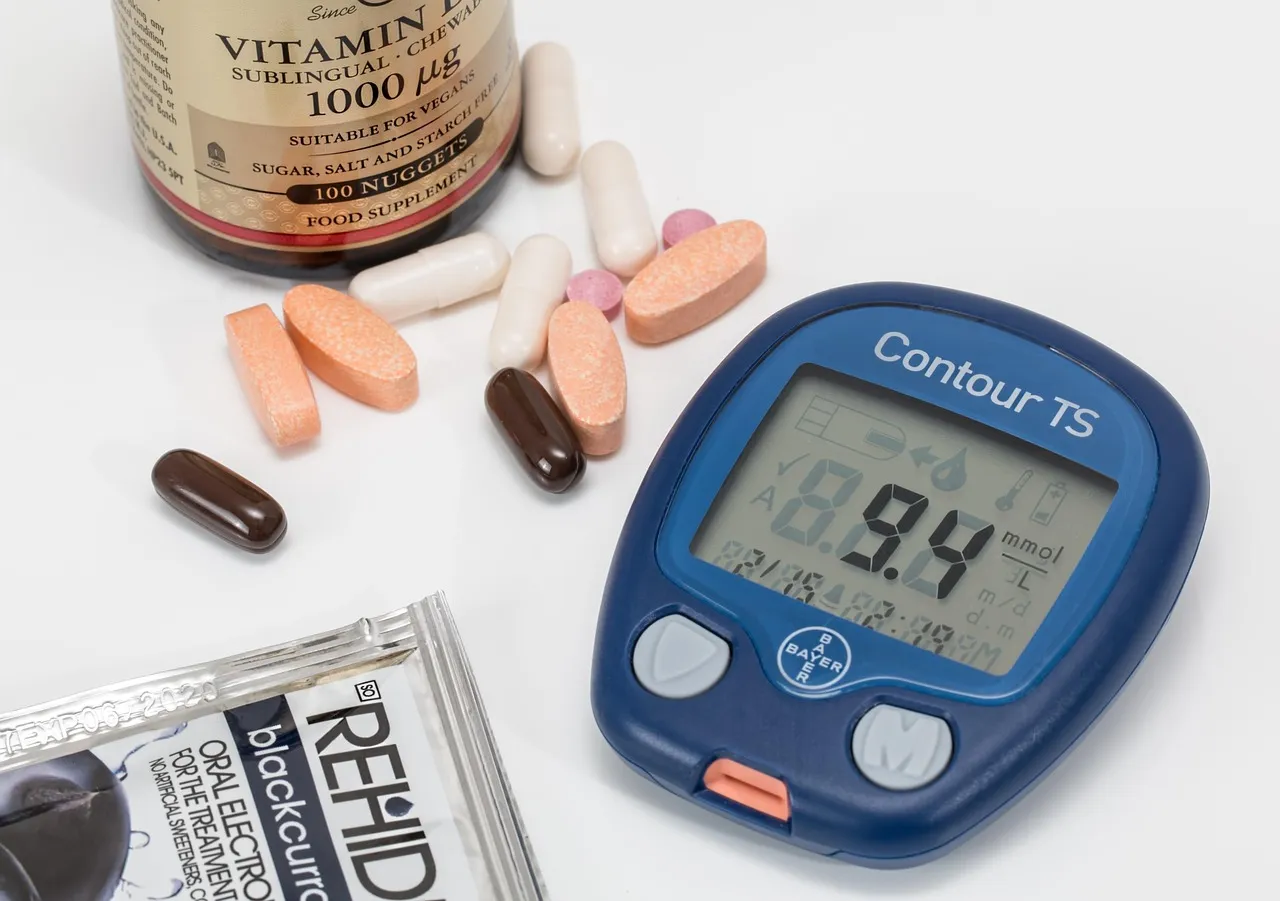
